Consumer Driven Six Sigma at Ford
|
|
ICMR HOME | Case Studies Collection
Case Details:
Case Code : OPER041
Case Length : 12 Pages
Period : 1998 - 2004
Organization : Ford Motor Company
Pub Date : 2004
Teaching Note :Not Available Countries : USA
Industry : Automobile
To download Consumer Driven Six Sigma at Ford case study
(Case Code: OPER041) click on the button below, and select the case from the list of available cases:
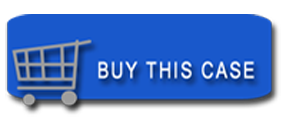
Price:
For delivery in electronic format: Rs. 400;
For delivery through courier (within India): Rs. 400 +Shipping & Handling Charges extra
» Operations Case Studies
» Case Studies Collection
» ICMR HOME
» View Detailed Pricing Info
» How To Order This Case » Business Case Studies » Case Studies by Area
» Case Studies by Industry
» Case Studies by Company
Please note:
This case study was compiled from published sources, and is intended to be used as a basis for class discussion. It is not intended to illustrate either effective or ineffective handling of a management situation. Nor is it a primary information source.
Chat with us

Please leave your feedback
|

<< Previous
Birth of Six Sigma
The journey towards Six Sigma quality at Ford began in late 1999, when Phong Vu
(Vu), Director of Quality for Global Truck Business was looking for innovative
approaches to improve the quality of Ford's vehicles. The answer was Six Sigma,
a data driven statistical technique, invented by Motorola in the 1980s and
implemented by companies like General Electric (Refer Exhibit I for a concept
note on Six Sigma).
Vu conducted research on leading companies which had implemented Six Sigma to
develop an understanding of its implementation process and its benefits. Vu then
suggested to Ford's management that the Six Sigma quality improvement program be
taken up.
|
|
The suggestion was accepted and the management decided
to launch Six Sigma, with the dual objectives of enhancing vehicle quality
and improving customer satisfaction levels. Accordingly, the initiative was
called 'Consumer-driven Six Sigma'.
|
Ford found that in the manufacture of a car, there existed about 20,000
opportunities for defects. Through Six Sigma, the company aimed at
reducing the defect rate to just one defect for every 14.8 vehicles.
Commenting on the motive for launching Six Sigma, Henry Wallace, Chief
Financial Officer of Ford said, "We have a very strong desire to improve
our level of customer satisfaction and we found we were doing
incrementally better and not moving the needle to the extent that we
wanted. So we looked for something that would really give us a quantum
leap forward."6 The implementation of Six Sigma required both on-the-job and
off-the-job training of employees. |
The Six Sigma projects had to pass through a
standard methodology known as the DMAIC (Define, Measure, Analyze, Improve and
Control) cycle, which formed the integral part of the project.
Training
The first step for implementing Six Sigma was the training of employees. By
January 2000, the top 50 executives of Ford, including CEO Jacques Nasser, had
received executive training. Executive Training was also imparted to 200 other
officials of the company which included the top management group, an officers
group and a leadership group...
Excerpts >>
|
|